原著: Matias Navarro (威立雅水务技术)
改编并翻译: Kok Fong Tiyo (威立雅水务技术)
制药公司的碳足迹
研究显示,全球制药业的碳排放量总计约5.2亿吨,超过汽车制造业的4.64亿吨。尽管制药市场比汽车制造市场小28%,但其污染水平却高出13%。
由于消费者、投资者和监管机构对全球气候问题的日益关注,生物技术和制药行业正在积极减少温室气体 (GHG) 的排放。这些行业通过评估其生产设施及研发实验室对环境的影响,专注于可持续实践和节省成本的机会。其中注射用水(WFI)的生产被确定为一个重要的碳排放源。
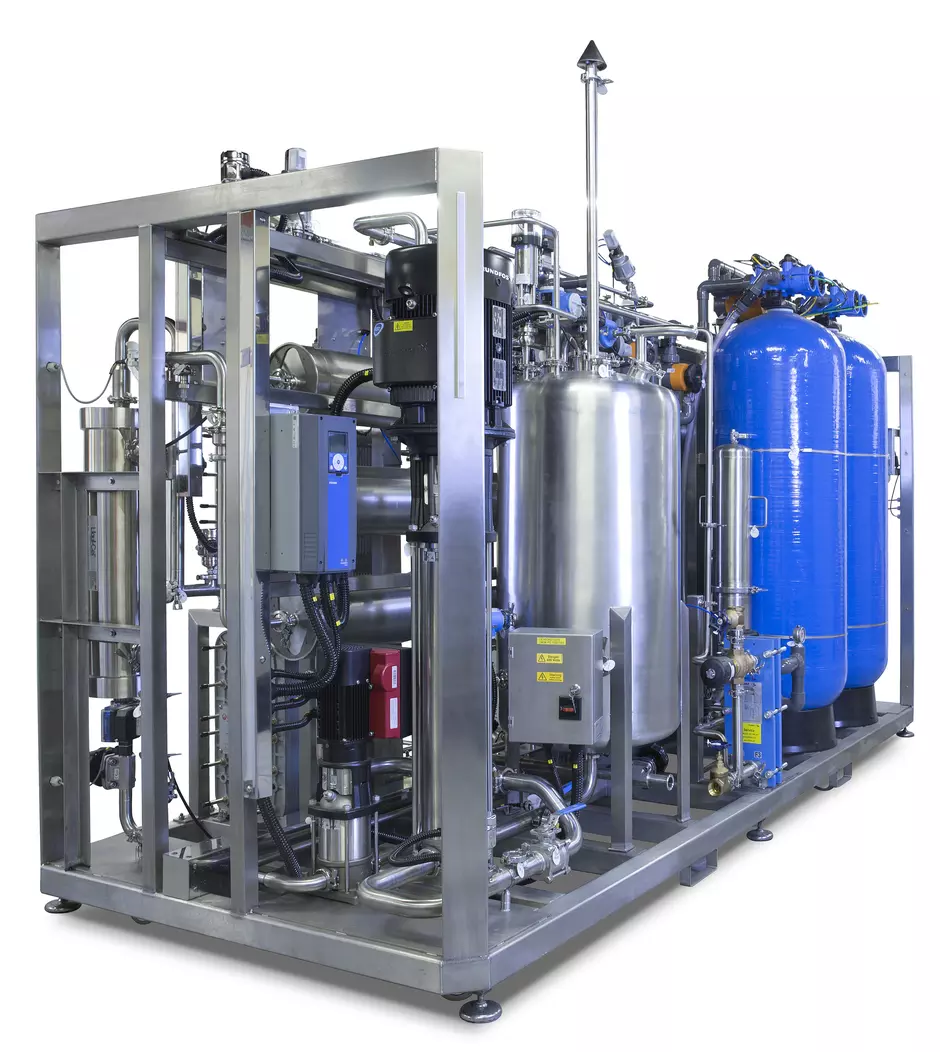
为实现净零排放(平衡排放的温室气体和清除温室气体),制药制造商正在从高能耗的高温注射用水系统转向可持续性的膜法注射用水系统。这一项转变不仅,减少了对化石燃料的依赖,并符合药物监管和可持续生产承诺,同时利用再生能源电力,为行业的绿色转型铺平道路。
注射用水生产的脱碳策略
制药业正通过重新评估和更新其制造工艺来减少碳足迹。这包括采用确保符合法规与降低微生物污染的技术,同时也能提高能源效率和使用绿色能源。此战略性的转变对于制药业实现碳减排目标及提高整体环境绩效至关重要。
注射用水 (WFI) 是一种高度纯化的无菌水,广泛用于药物制造和生物加工,对行业的碳足迹占了一定的比例。 WFI 对于各种制药工艺至关重要,包括注射药物和生物药物的生产,以及生物技术研究和生物药品的制造与应用(例如清洁、稀释工艺)。
随着市场对 WFI 的需求激增,特别是随着生物疫苗产量及逐渐普及化的信使核糖核酸 (mRNA) 生物技术,将使其成为制药行业减低成本和碳排放的主要驱动因素。传统的注射用水生产主要集中在使用高能耗的蒸馏方法,该方法自 20 世纪 70 年代以来一直是业内的标准。蒸馏法,尤其是多效 (ME) 蒸馏和蒸汽压缩 (VC) 蒸馏工艺,和在纯化水储存与分配系统中持续的使用大量的工业蒸汽,也是制药行业碳排放的来源。
减少注射用水碳排放量的重点应该注重于降低蒸馏法的使用,并转向低碳排放的生产方法,例如低温和常温系统的膜法注射用水。这些新技术有望与减碳目标保持一致,并节省成本。如果广泛采用,有可能满足全球制药业对脱碳的需求。
鉴于上述多重因素,注射用水(WFI)生产的改革势在必行。历史上,注射用水生产仅限于蒸馏法,以满足药品无菌监管标准。然而,因膜技术的突破与稳健的运行功效、法规的转变和可持续性的绿色目标为基础、为膜法注射用水的使用铺平了道路。
注射用水生产
自2017年以来,除中国药典外,大多数全球药典都允许使用非蒸馏法生产注射用水。欧洲药典里对注射用水通则的改革大幅度的承认了膜技术的使用,以确保制药用水的安全;而无需依靠高能耗的传统蒸馏法一并带来的高能源成本和碳排放。在国内,在不久的将来,膜法注射用水将成为国家药典的一项新指标。目的不仅仅是实现低碳排放的标准,也为制药业,尤其是大输液制造带来巨大的低成本效应。
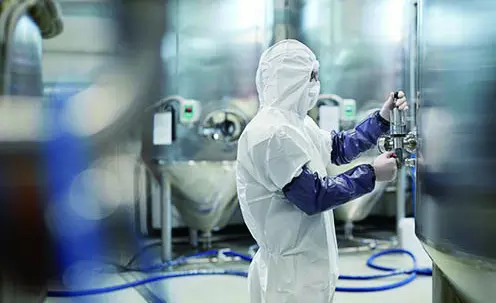
膜法注射用水提供了不依赖常态高温、高热量的纯水净化解决方案,从而直接减少制药业对化石燃料的依赖。此外,日益重视的再生能源使用,以及实施征收碳排放税的潜力使得常温注射用水系统更具吸引力。这将会让制药业带来良好的投资回报。
尽管膜法注射用水对制药业有着明显的经济效益,但对于相对保守的制药市场对其使用率预计会有一些时间上的过渡期。在这过渡期内,膜法注射用水只能满足一小部分制药商的用水需求。
膜法注射用水
与传统的工业蒸汽加热蒸馏法相比,采用反渗透膜(RO) 的膜法注射用水(WFI) 系统可显著节省能源和运行成本。 反渗透膜是一种利用强大的压力迫使纯水通过半透膜的过滤,无需高温把纯水蒸发到蒸汽,再使用冷凝水将纯蒸汽凝结为高温注射用水。因此膜法注射用水也被称为冷或常温注射用水。膜结合去离子技术普遍用于半导体制造行业等要求极严格的超纯水系统中,并且自 20 世纪 80 年代中期以来一直是制药行业生产纯水的一部分。
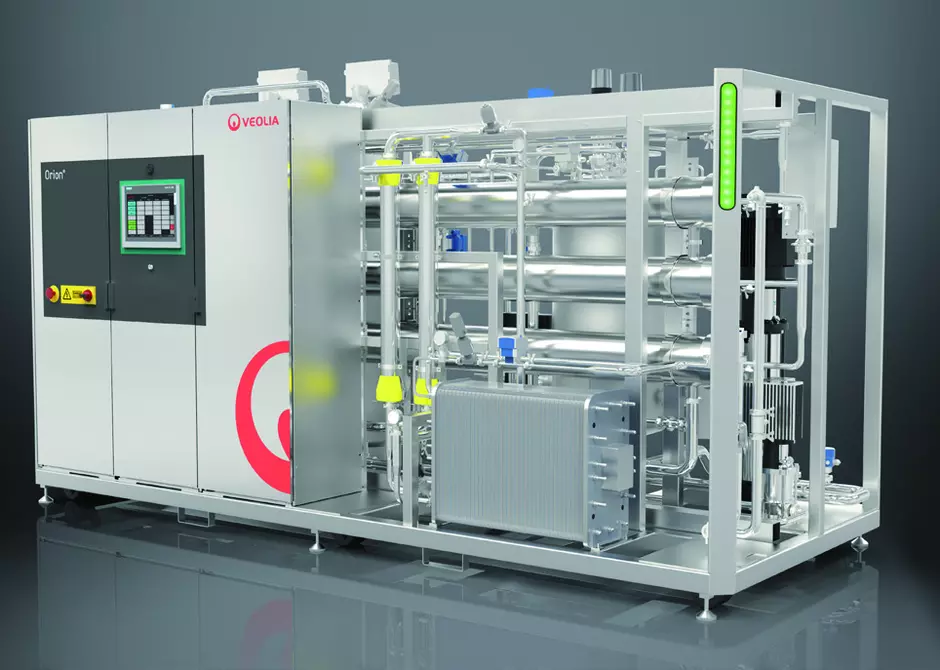
冷注射用水系统比蒸汽压缩蒸馏节省高达 50% 的电力消耗;与多效蒸馏相比,整体能源用量亦显著减少。这些系统通过结合电动泵和集成反渗透技术、电去离子和超滤膜等等的持续净化过程,将软化、脱氯水转化为注射用水。在这过程中,二氧化碳排放量更少,并能根据医药用水的产量来调节泵压力,从而提高系统的能源使用效率和寿命。
此外,膜法射用水系统可以有效解决微生物风险。系统使用巴氏消毒来控制生物膜的形成,大大地降低化学品带来的污染。而且其设计也大大地减少废水排放,从而减少了水资源浪费和环境影响。这些系统还避免了高温注射用水所需的高能耗加热和冷却工艺,直接降低了运营成本和碳排放。再者,膜法射用水系统可配置常温储存和配送,过程中使用臭氧进行常态消毒,进一步降低能源使用以及微生物的污染风险。如果,系统中配有有效制程控制,例如:TOC, 快速微生物检测仪等等,能对异常运作的系统做出快速报警和纠正,来减低药物质量品质管理的压力。
注射用水的温度与法规
您是否正在审视注射用水(WFI)系统的最优温度?是选择65°C、80°C还是85°C?事实上,WFI系统并不存在单一的 “最优” 温度。制药业可以自行选择任何温度来保留、生产和输送WFI。因为,制药用水温度不在药典的规定以内。
然而,如果企业在用户需求规范(URS)或标准操作程序(SOP)中指定了注射用水的温度,则必须遵循该温度。这种“用户定义”的温度成为合规问题,可能会受到药品监督管理局的强制执行,尽管这不是各国药典的要求。
从历史上看,较高的温度一直被认为有利于WFI系统中的微生物控制。然而,诸如臭氧处理等先进方法,即使在温度常温下也能提供强大的微生物控制。臭氧是一种强效氧化剂,在足够的接触时间内能够有效地将有机物(包括微生物、真菌和病原体)氧化并将其分解。
评估WFI系统温度时,需综合考量以下因素:
- 温度设定的实际需求与影响
- 不同温度方案的成本差异
- 相关文档的合规性要求
请注意,温度选择具有灵活性,重点在于明确其设计目的和潜在影响。
总体而言,膜法注射用水系统由于低营运成本、减少微生物污染以及符合可持续发展和净零排放目标而变得越来越普遍。和传统蒸馏比较膜法注射用水提供了更实用且更高效的替代方案,并支持制药行业转向高度持续发展的成果。
迈向膜法注射用水的转型
实现净零排放以及解决经济压力的双重目标推动了使用采用膜发注射用水 (WFI) 系统的运用。这种迈向全电动、降低燃烧化石燃料(低碳)产生注射用水的转变与行业内脱碳的努力相一致。其中还包含了采用在地太阳能发电和微电网的可能。现阶段制药行业对常温WFI可能还存在一些疑虑(微生物风险),但有效的膜法系统的设计、规划、验证与运行,再加上大幅度减低成本,实现净零排放目标的好处使其成为一种可行的权衡。
膜法注射用水系统因使用电力驱动,可采用再生能源,显著的推进减碳排放的目标。许多制药公司致力于使用绿色能源为其生产与运营提供动力,而偏好使用可再生能源和太阳能发电等技术。这种方法不仅降低了电力成本,而且符合国内“双碳”目标的规范,以达到高能源效应能和未来零碳排放的愿景。这些战略是行业目标的核心,可提高药品制造的竞争力和可持续性。
使用低碳注射用水
实现净零目标需要全面的工艺应用与健全的财务策略,以便从传统的蒸汽过渡到膜法注射用水系统。制药企业应首选更换高能耗的蒸馏注射用水系统;虽然膜法射用水系统的前期成本可能偏高,但其卓越的节能效率可以带来显著的成本效益。在一些国家,使用绿色能源可带来的可观的碳税优惠,进一步缩短系统的投资回报期。
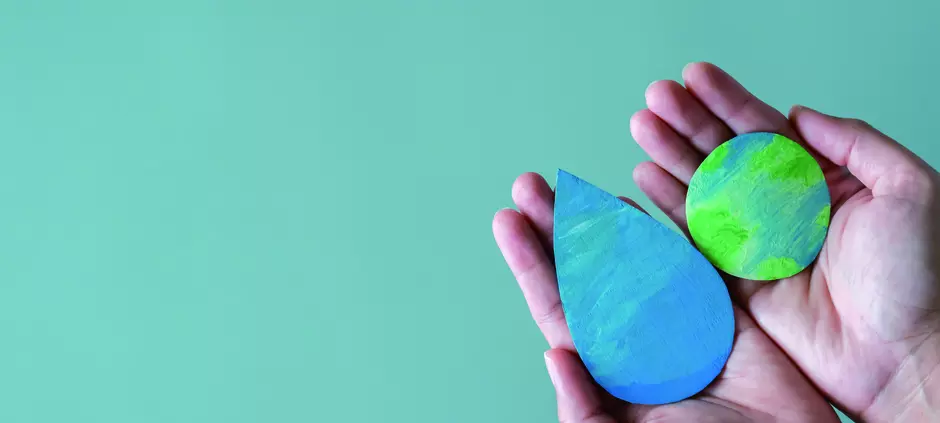
对于一些企业背负着严格的低碳政策,也同时面对有限购买新系统的预算,可转向金融机构洽谈融资的可能;以减少能源开支所节约的运作资金来补贴融资成本,从而降低药品生产成本。此外,制药企业可以通过威立雅所提供的 “Water-as-a-Service (WaaS)” 服务。此项服务以按用水付费的方式提供膜法注射用水生产、技术与营运上的支持。以”零”投资成本为企业带来快速的转型,并将系统维护和责任转接给服务供应商。这些策略不但促进了膜法注射用水系统的采用,同时也帮助企业达到绿色环境目标和财务自主的可行性。
膜法注射用水具有良好的商业意义
由于制药行业的利润趋紧和竞争压力的日益加大,采用膜法注射用水 (WFI) 系统具有良好的商业效益。随着化石能源成本持续攀升和普遍社会对碳排放施加的压力不断增大,注射用水生产工艺的现代化不仅可以有效的控制支出,还能显著减少企业的碳足迹,从而提供快速而有效的成本收益。与传统蒸馏器相比,膜法注射用水系统不仅资本支出低于43%,而且更能降低预处理成本,直接节省可观的运营费用。
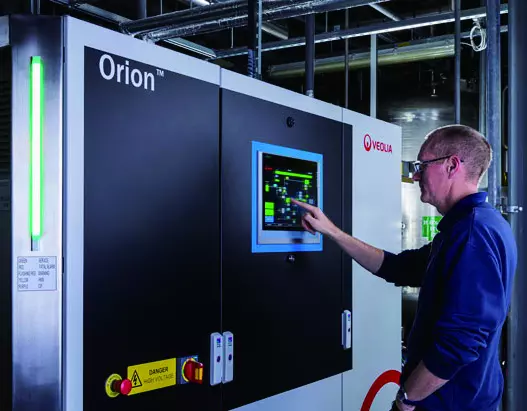
过渡到膜法注射用水系统符合碳净零目标,并避免长期锁定因使用高能耗技术相关的高碳排放成本。除了直接的经济收益外,还可以提升公司的声誉,增加商誉,并加强与注重可持续发展的利益相关者之间的关系。
使用蒸馏系统抑或改用膜法注射用水系统的决定取决于成本收益。推迟此项转型可能会积累环境和公司利润的隐性成本,从而增加气候、企业在市场上的声誉风险。由于消费者、投资者和监管机构要求该行业在可持续实践方面承担更大责任,因此利用膜法注射用水系统降低气候变化的未来不仅是可取的,而且是必要的。
结论
在这日新月异的时代,制药专业人员迅速推进了医药科学和治疗方法,展示了他们满足全球对药物紧迫需求的能力。同时,制药企业在环境、社会和治理 (ESG)的提倡也凸显净零排放面对绿色环境的重要性。膜法注射用水 (WFI) 系统更被解读为更清洁、更可持续的运营提供了实用且高效率的好处。制药行业现在必须运用更进一步的验证和奉献精神来加速脱碳进程,利用其优势对环境产生正面影响。
联络威立雅专家团队
威立雅水务技术中国
于飞
+86 135 0184 7807
[email protected]